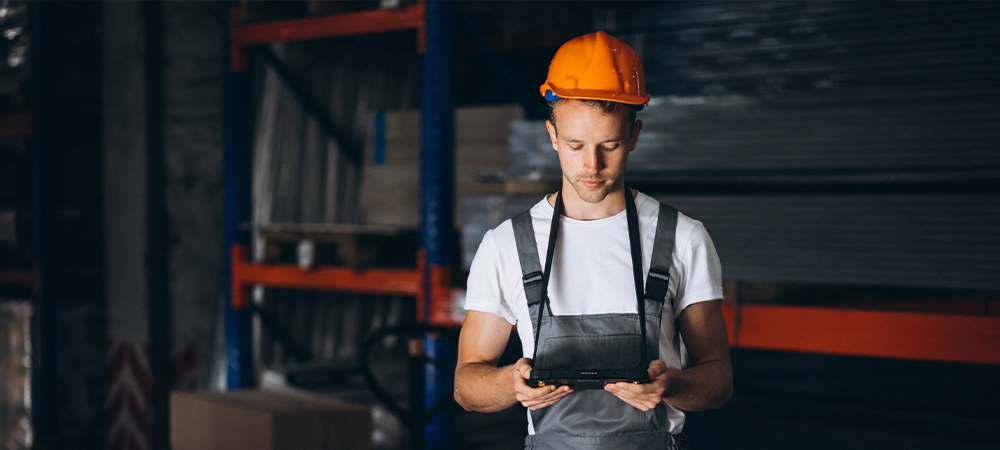
Global management of Health and Safety at the click of a mouse
Health and safety management within large industrial organizations requires a dual approach.
On the one hand, managers must enforce specific laws and regulations with which the organization is equipped. We can define this approach as “top–down“, that is from top to bottom. On the other hand, those who really live the factory every day should report the real and potential dangers, so that those who manage production can constantly improve organizational measures.We can define this approach as “bottom-up“, that is from bottom to top.
The first approach is mandatory by law and basically does not require the management of large quantities of information. It is a “qualitative” approach, in which communication is made through official documents (plans, provisions, etc.) and service orders. Its main aim is not so much the improvement of the real working conditions, but to comply with the mandatory provisions of the law, so as not to have problems with the inspectors of the national health services. I know I shouldn’t write such a thing, but anyone who has worked in the industrial world knows exactly what I’m talking about. The second approach, however, is not mandatory, but it is so important that companies have done everything to make it a standard, forcing each other to respect the principle of constantly collecting information from below, verifying it, identifying new ways to reduce the risks of any type and evaluate the changes introduced to understand if it is possible to do even better.
The principle is that of continuous improvement and is the basis of each Occupational Safety Management System (SGSL).
The main method that companies have found to oblige each other to apply this principle with regard to the health and safety of workers has been the request for certification to the international standard ISO 18001 (OHSAS – Occupational Health and Safety Assessment Series) that the main producers make to their suppliers and they cascade onto their supply chain.
The same thing has been done for the health and safety of the environment, through the mutual request for adhesion to the ISO 14001 standard and the creation of an Environmental Management System (EMS). Furthermore, both of these systems have often been included in more specific and restrictive rules that concern a particular industrial group, such as World Class Manufacturing which provides very advanced continuous improvement systems for both Safety pillar and Environment pillar.
The origin of this “bottom-up” approach is not such a recent novelty. Already in the 1960s, “homogeneous groups” were born at the FIAT factory in Mirafiori, in which workers and workshop managers discussed together possible improvements of the work areas healthiness.In 2007 I had happened to work on the production of a documentary that collected the memories of Ivar Oddone, the occupational doctor who had set maps in which workers signaled possible risks based on their sensory experience (noises, smells, visual perception of dangers, etc.). Discovering that many years before such methodologies had been applied in what, at the time, was the largest factory in Europe, had really surprised me.
So, when in 2008 I was asked to provide employees of the same factory with a distance training system relating to the obligations of the ISO 14001 standard on continuous environmental improvement, I realized that the same approach, after several decades dominated in the West by a rigid technocratic management was at the basis of the most modern continuous improvement practices in the field of the Environment and Health and Safety in the workplace.
The first request for the implementation of a software system for the collection and analysis of data relating to Safety and Environment then came to me in 2014 from Elica SpA, the Italian company, world leader in the production of kitchen hoods. The way chosen by Exagogica to provide the necessary tool to coordinate the activity in all Italian plants was to develop a specific module of our Panoptikon system. This made it possible to create a data collection system by exploiting a mapping of the production lines already present in the manpower use management modules.
The HSE module came into use in Elica the following year and since then has been used to manage the collection of all reports and, above all, to process the risk indicators of the various production areas, using the tools of the Heinrich Pyramid and the S matrix.
This tool has already been adopted the following year by the main Italian plant of Denso, belonging to the Japanese automotive multinational of the Toyota group. For the implementation in Denso, in addition to the normal developments foreseen in the product roadmap, we have implemented a sophisticated system of planning, execution and analysis of internal audits.
In 2018 Exagogica then received from Denso TEC a request to create a tool with which to manage the Health and Safety activities at a global level in its 18 factories. Starting from the modules already implemented, we have carried out a customization that makes the Denso TEC system a best practice for the implementation of a safety management system based on the continuous improvement approach.
The system provided by Exagogica, in fact, allows easy reporting of the safety tags (unsafe act and unsafe condition) both for spontaneous reporting and following execution of an inspection or safety audit. The tags are analyzed statistically in order to define the areas of greatest risk and on which to deepen the analysis activities to improve safety conditions.
The implemented system provides also management of accidents, first aid, near miss, ergonomic injuries, accidents en route, which are the subject of an in-depth analysis for the search of the root cause through the step-by-step guided application of traditional methods of analysis: 5W +1H, Ishikawa, 5Whys. The analysis procedure is integrated with the application of countermeasures.Once identified, these are transmitted to those in charge who must apply them in their specific production area and their implementation is tracked and monitored through the system.
Exagogica’s HSE module also allows the management of transversalization, that is, the planning of the implementation of countermeasures in areas similar to the one in which they were initially introduced, as well as allowing easy management of best practices, which are shared globally among all the factories of the group.
The real strength of the system, however, lies in the management of KPIs, the Key Performance Indicators relating to security, which are automatically aggregated from the single department to the countries and overall values. The fully automated management of these values, which derive from the transactional activity of all operators involved, allows full and real implementation of a continuous safety improvement system based on the constant collection of information of those who live the life of the plant every day.
After a few months of running-in, the system we implemented in Denso TEC became the group’s standard in July 2019. From that moment it ensures the constant increase in safety standards for over 8,000 workers and this for me is not only a satisfaction linked to the conclusion of a long research path, but a real source of pride for the use of the software that we have created.
Alessandro Obino, CEO Exagogica
All rights reserved